UAV.com Staff Report
An advanced, high-demand customer needs new capability – fast. What's the best way to deliver and ensure maximum performance in the minimum time?
One answer is with additive manufacturing, or AM.
Being the world leader in any area of business can be precarious. Competitors are always nipping at your heels. Copycat products are developed. For General Atomics Aeronautical Systems, Inc., being the world leader in unmanned aircraft systems has required the company to continually refine how it manufactures its products to respond to orders like these.
That's why this key area of manufacturing has evolved dramatically over the past decade.
AM is a process in which engineers take a three-dimensional computer-aided design model and virtually slice it into thousands of layers. This is sent to a printer, in which material is added one layer at a time to create a three-dimensional object.
Like most aircraft manufacturers, GA-ASI works in low-volume, high-mix, and high-quality parts. That fits into the wheelhouse of AM, and as more structurally capable materials have been introduced, GA-ASI has been able to produce flight-ready parts for its line of unmanned aerial systems. This undertaking drove the creation of the company's AM department and team in 2018, which has evolved into a production-ready Center of Excellence, or CoE.
GA-ASI's CoE for Additive Design and Manufacturing was established in 2021 with a mission to enable and accelerate the adoption of AM technologies and integrate them into its engineering design and manufacturing operations.
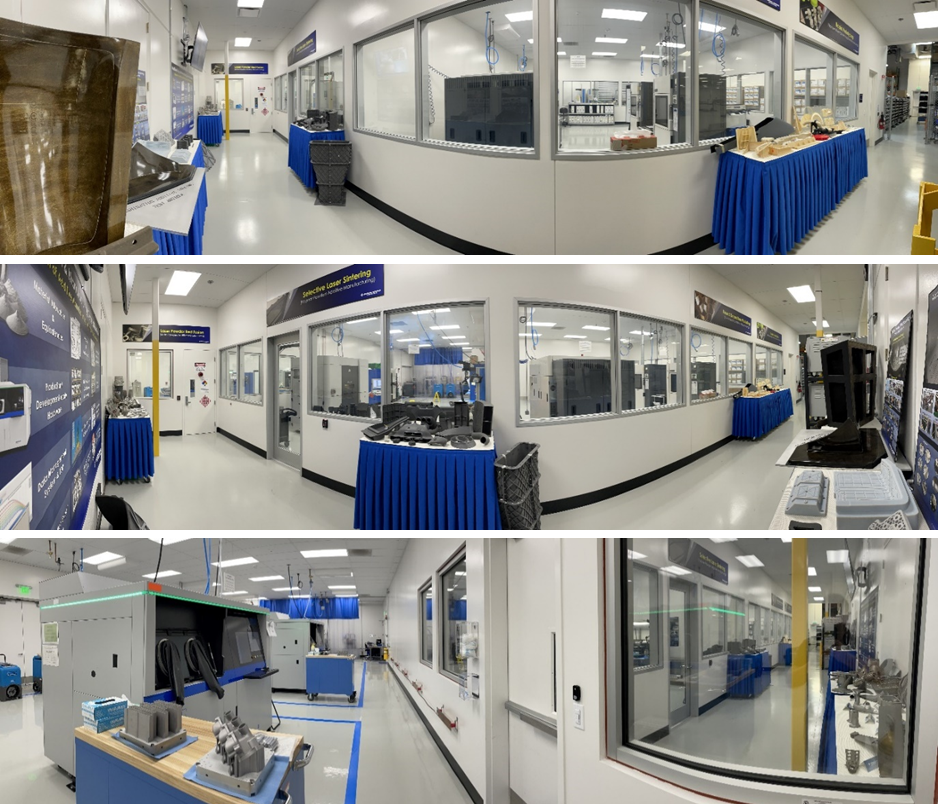
Why do this? Primarily to consolidate knowledge and resources while increasing business efficiencies, accelerating implementation, and delivering the highest value possible to customers. AM streamlines the time from product launch to market readiness by shortening the design and manufacturing process, increasing productivity, reducing assembly costs, and providing cost advantages through low-rate production.
Additionally, AM lets engineers manufacture ever more complex and unitized designs, leading to performance improvements and significant cost reductions.
AM at GA-ASI
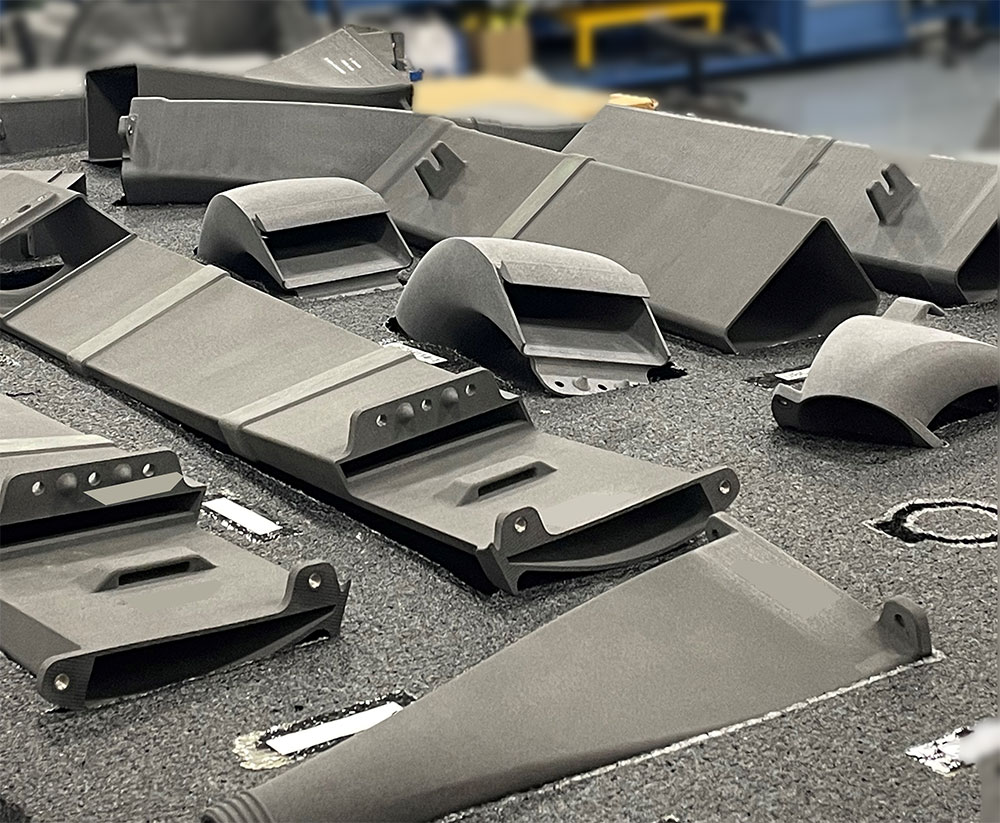
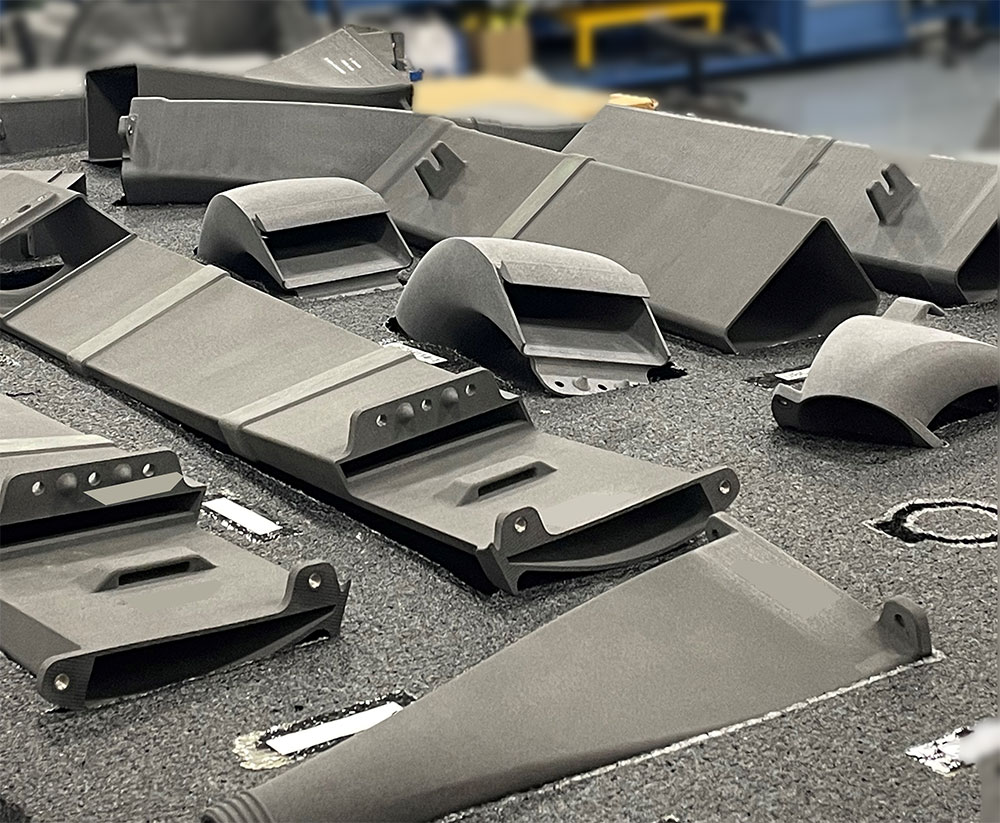
"GA-ASI is continually looking for ways to enable, accelerate, and integrate Additive Manufacturing technologies into our designs, our operations, and our products," says GA-ASI President David R. Alexander. "Through our AM Center of Excellence, we're using a structured and stringent qualification process for AM applications that delivers a positive business case for us over conventional manufacturing methods. Through a comprehensive and holistic approach, our team of AM professionals is working to increase the adoption of AM parts for the benefit of our aircraft and, ultimately, our customers."
For GA-ASI's new MQ-9B line of UAS, which includes the SkyGuardian® and SeaGuardian®, AM parts have saved the company over $2 million in tooling costs and over $300,000 per aircraft in recurring cost avoidance by integrating over 240 AM parts onto those aircraft platforms alone. Those parts are primarily tertiary structures, including air management ducting and manifolds, covers, intakes, enclosures, and shields that use high-strength polymers, composite polymers, and metals. But the company is also developing AM parts of increasing criticality to flight itself.
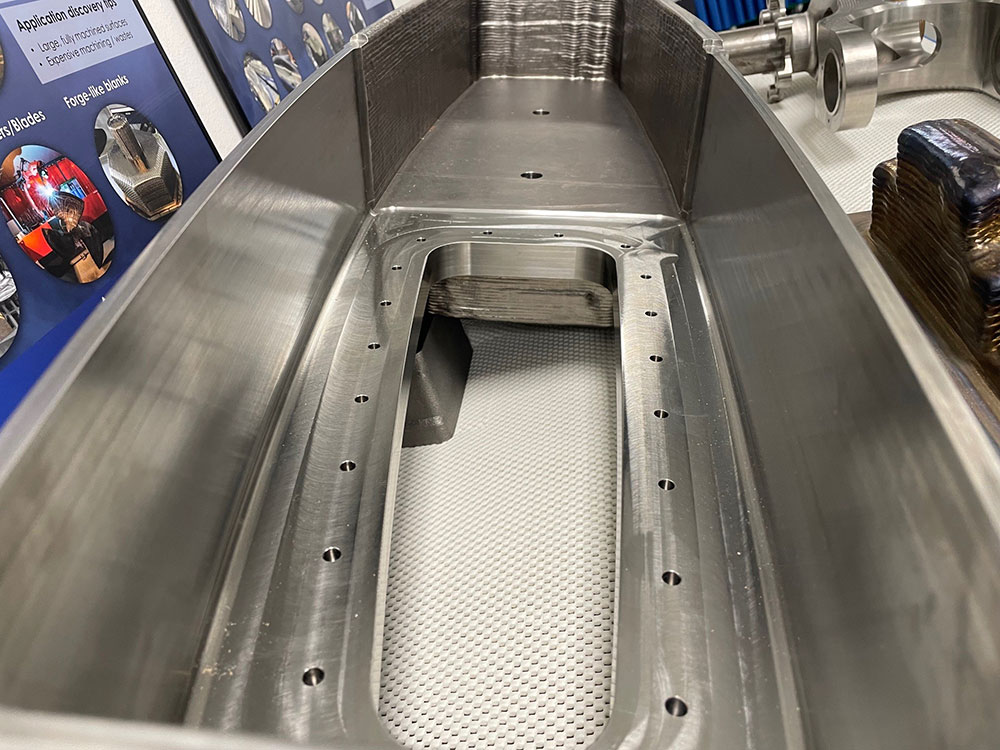
"After years of engineering testing and substantiation, we are now introducing mission-critical structural AM components using titanium in our next-generation platforms," says Steve Fournier, GA-ASI senior manager for AM and the AM Center of Excellence.
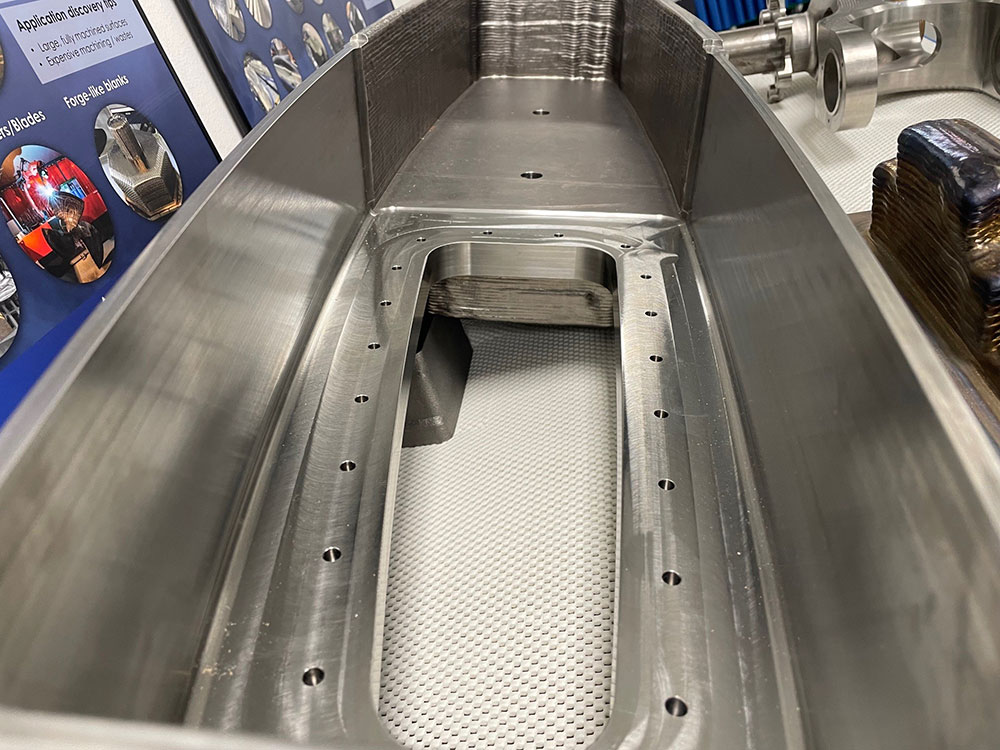
Overall, the number of AM applications is growing rapidly, fueled by the AM ecosystem established at GA-ASI. As a result, the company already has more than 10,000 additively manufactured components on the aircraft it has produced, and the SkyGuardian and SeaGuardian models are leading the industry in the use of AM parts.
AM also reduces the cost impact to GA-ASI customers by lowering the financial burden to achieve operational performance of its UAS products in both flight hardware and tooling.
"To me, the most important benefit of AM for our customer is the improvements in time to market for our products," Fournier says. "It also allows more complex and integrated designs that improve UAS performance; and as a flexible manufacturing solution, AM can solve many supply chain and sustainability issues for our customers."
AM for Small UAS
GA-ASI is growing its business into a new area of unmanned systems known as Small UAS, or SUAS. As global militaries look to these SUAS platforms to provide new levels of capability, the value of AM is highlighted through its rapid prototyping capabilities as well as on the production line.
In late 2023, GA-ASI demonstrated a new advanced air-launched effect that was dropped from an MQ-20 Avenger® – a large jet-powered UAS also produced by GA-ASI. The airframe of the SUAS platform was 100 percent additively manufactured and was designed using advanced topology optimization and AI-driven technologies in partnership with Divergent Technologies in order to meet the captive carriage and ejection loads of the jet-powered aircraft with internal bays.
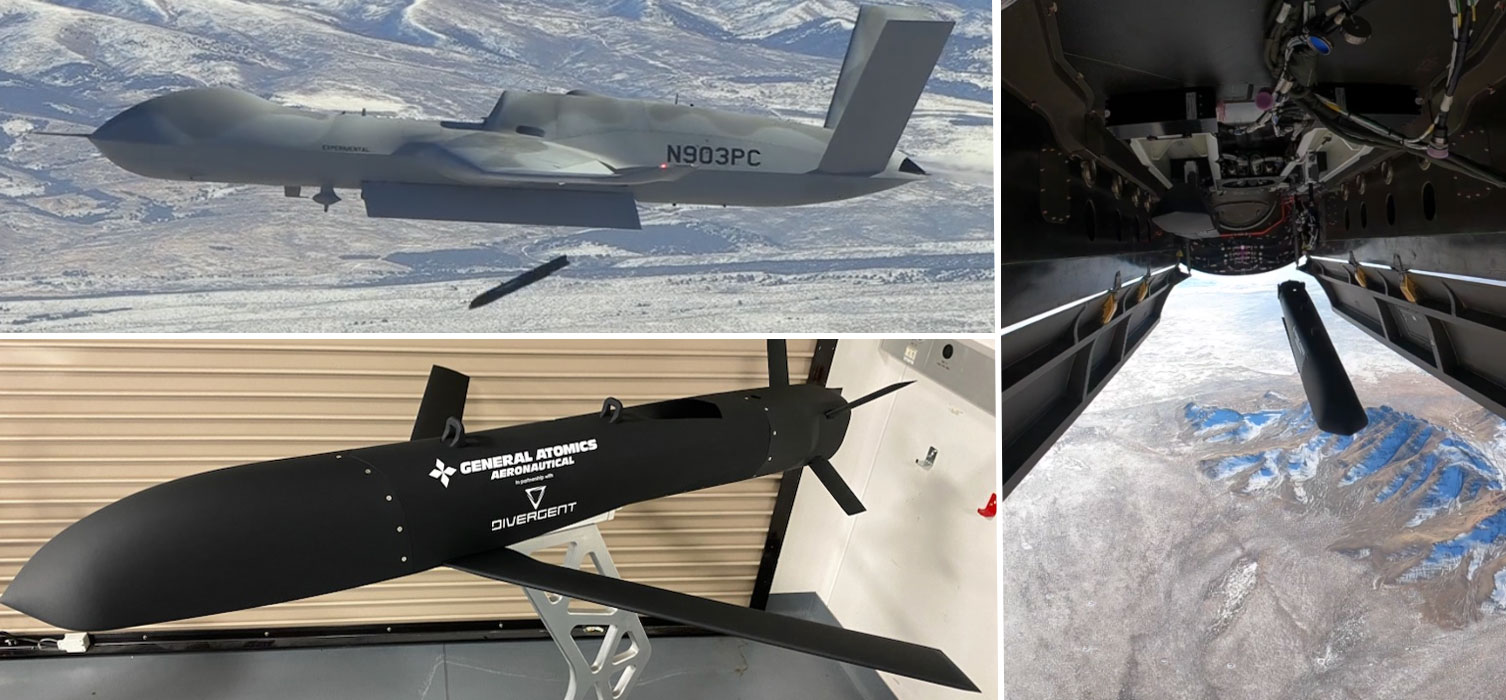
The demonstration showcased the cost, performance, and time-to-market efficiencies that can be realized when advanced design technologies and AM are incorporated early in the airframe development process and throughout the production of the vehicle. It was also an important step in validating the AM process and material properties for incorporation into future air systems to be employed by both manned and unmanned platforms.
GA-ASI has produced other SUAS, including a small folding-wing UAS called Sparrowhawk, designed to be an air-launched platform that can be recovered by its larger launch UAS in mid-flight. There's also the propeller-driven Eaglet. SUAS will be asked to perform some of the most dangerous assignments in the world – which is why global militaries are looking to unmanned aircraft to undertake them. If something happens to these aircraft, the life of a human pilot is not at risk.
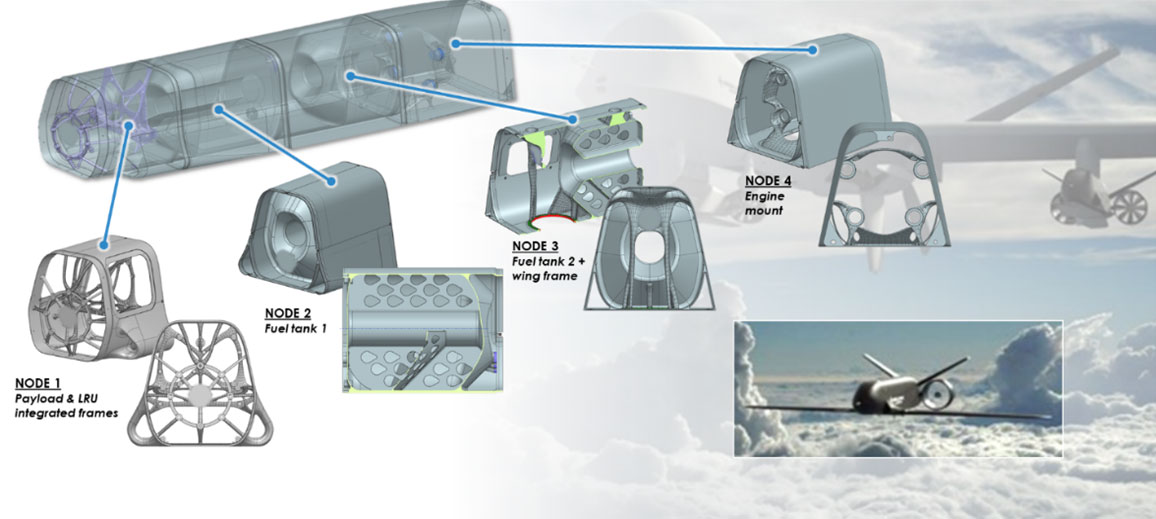
By the Numbers
To date, GA-ASI has developed over 350 flight-qualified AM parts and produces over 7,500 production AM parts annually that have successfully completed over 300,000 combined flight hours. The company expects its AM growth rate to rise from 15 to 25 percent per year.
"We demonstrated to ourselves, then to our management, and later to key customers, the many, often compounding benefits that additive technology can bring to programs, not just during the prototyping phase but also as low-rate initial production gets underway," explains Fournier.
Fournier says that GA-ASI differentiates between prototype and production projects to identify the right applications early on to drive the establishment of the elements of an AM ecosystem for application families that have a good chance of success.
"We ensure that proper business case assessments are performed before technical development moves forward," says Fournier.
In all, AM parts and processes are continuing to drive new levels of manufacturing efficiency for GA-ASI's product line.
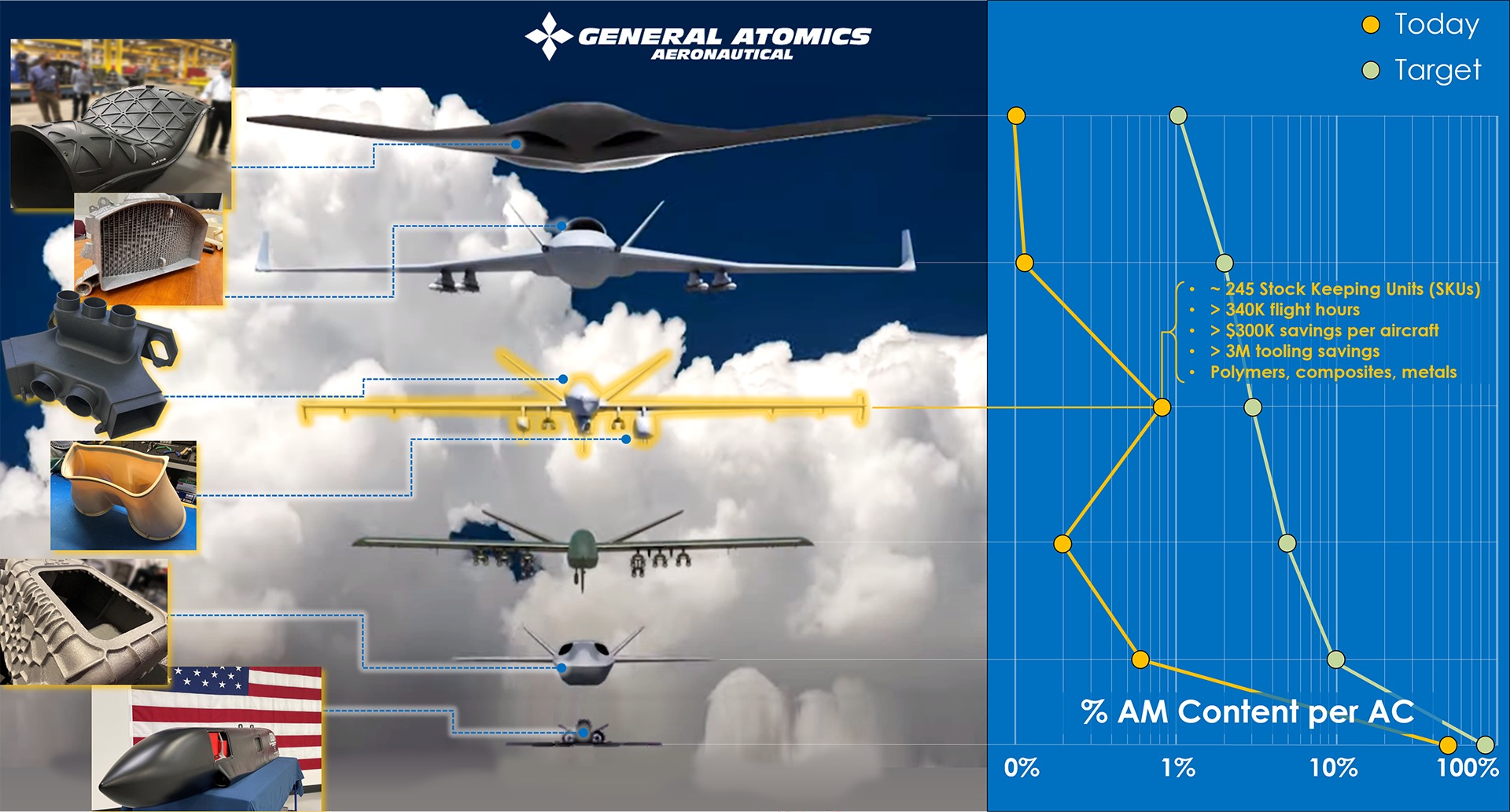
AM at GA-ASI: https://youtu.be/AMv26Vlj-Cw?si=N0RFn_x0WTZRWJ9z